Optical Coatings
Enhancing Light Control and Performance
Optical coating is a specialized process involving the application of an exceptionally thin film onto the surface of optical components. This film is meticulously engineered to either enhance the transmission of light, modify the reflective properties, or manipulate the polarization of emitted light. These coatings can range from straightforward metal sheets like aluminum to intricate dielectric coating consisting of precisely designed thin layers of materials with specific thicknesses, compositions, and layer counts.
Avantier specializes in applying thin films to optical components, which enhances light transmission, modifies reflection, or manipulates polarization. These coatings come in various types, including filter, beam splitter, high-reflective, low-reflective, and anti-reflection coatings, each serving distinct purposes. Cutting-edge technologies like IAD E-Beam, IBS, PARMS, and APS are employed in the production of these coatings. Currently, we have eight coating machines in our Vietnam factory.
Optical coatings have evolved with technological advancements, finding applications in various industries across different spectral regions.
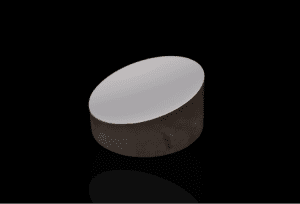
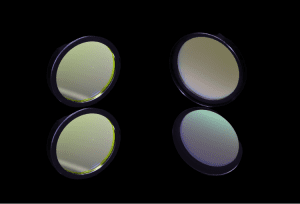
Type and Capabilities of our Optical Coatings
- Filters: Fluorescence, Dichroic, Narrow Bandpass, Multi-Bandpass, Notch, Edge (SWP and LWP)
- Anti-Reflection: Single Layer, High Efficiency Multi-Layer (Broadband), Laser V, Double Laser V
- High-Reflection: Utilizing internal reflection for high performance in optical applications
- Low Reflection: Maximizing light throughput, minimal reflection in optical applications including laser systems
- Beamsplitters: Polarizing, Non-Polarizing
- High Laser Damage Threshold: Anti-Reflection, High Reflection
- Ultrafast coatings with controlled group delay dispersion (GDD) for laser pulse compression
- ITO Conductive
- Mirrors: Protected and Enhanced Aluminum, Silver, and Gold; Hot and Cold Dielectric; Multi-Layer Dielectrics
- Tailored Designs: Build to Print, Custom Design and Development for UV, Visible, Infrared (NIR, MWIR, SWIR, LWIR)
- Hydrophobic Membrane
- Diamond-Like Carbon Coatings with High Hardness and Resistance to Scratches and Corrosion
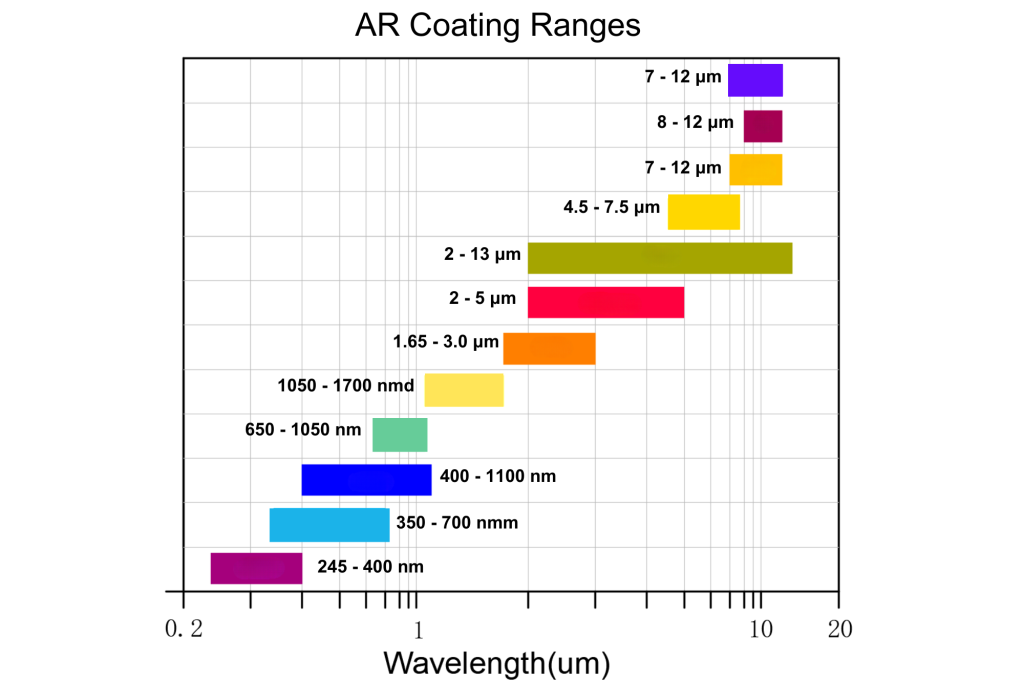
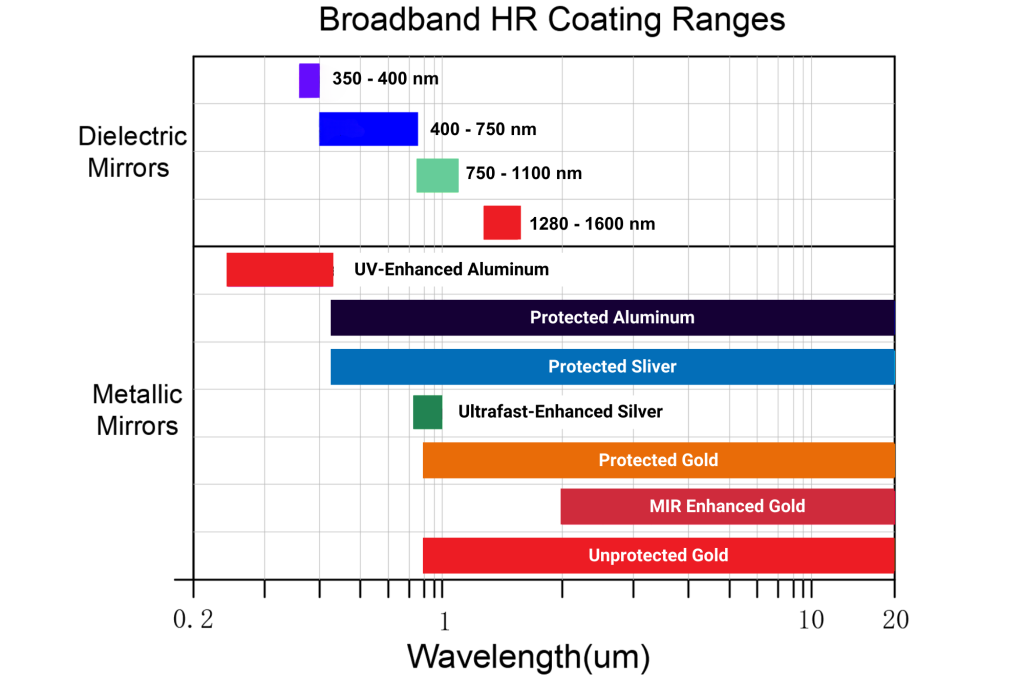
Cutting-Edge Coating Technologies
A variety of coating technologies are employed, each offering unique benefits and suitability for specific applications. Here are some widely used optical coating technologies:
- Ion Assisted Electron Beam (IAD E-Beam) Evaporative Deposition: This method vaporizes materials in a vacuum using an electron gun, allowing flexible coating designs with diverse materials and large chambers. It is cost-effective and versatile, though it may have performance trade-offs in different spectral regions.
- Ion Beam Sputtering (IBS): IBS produces high-quality, stable optical coatings with precise control over oxidation, layer development, and energy input. It offers repeatability and durability but is costlier and slower than some methods.
- Plasma-Assisted Reactive Magnetron Sputtering (PARMS): PARMS uses glow discharge plasma to create tough, dense coatings. It balances optical performance and volume throughput, making it ideal for fluorescent optical filters.
- Advanced Plasma Sputtering (APS): APS enhances IAD E-Beam with advanced automation, providing smooth, dense, consistent coatings. It serves as an intermediate solution between IBS and IAD E-Beam deposition.
The field of optical coatings has witnessed remarkable growth driven by technological advancements and increasing demand across various industries, including electronics and semiconductors. Optical coatings, used in products ranging from eyeglasses to camera lenses, represent a versatile technology with a wide range of applications and benefits that should not be underestimated.
Optical Coating Testing Equipment & Metrology
- Agilent Cary 7000 Spectrophotometer, PerkinElmer LAMBDA Spectrophotometer, PerkinElmer FT-IR, Olympus MX51 DIC Microscopes for Spectroscopic Analysis
- ZYGO NewView 9000 for Surface Roughness Metrology
- Environmental Test Chambers: Temperature, Humidity, Salt Spray
- UltraFast Innovations White Light Interferometer for GDD measurements
- Automated Abrasion Tester for Durability
- Atomic Force Microscopy (AFM)
To learn more about Optical Metrology Solutions, visit the “Optical Metrology Services” page.
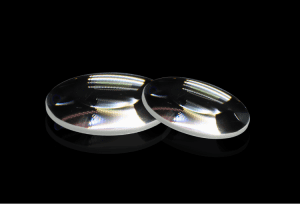
Materials for Optical Coatings
Optical coatings serve various purposes, enhancing the performance of optical components.
- Anti-Reflective Coatings minimize unwanted reflections, reducing the reflection of incident light from about 4% for uncoated glass to less than 0.1% with specific AR coatings. These coatings are available in both broadband and narrowband options, covering a wide wavelength range, with magnesium fluoride (MgF2) being a popular choice
- Reflective Coatings increase surface reflectivity, with metal coatings like aluminum reflecting 88-92% of visible light and silver reflecting 95-99% in the far infrared region. Dielectric coatings can achieve reflectivity up to 99.9% through alternating layers of high- index materials (such as ZnS or TiO2) and low-index materials (such as MgF2 or SiO2).
- Polarizing Coatings are created through interference effects in multi-layer dielectric coatings or thin films of birefringent materials. These coatings are designed to function at specific angles and can replace polarizing prisms in optical assemblies.
- Transparent Conductive Coatings offer a combination of high light transmission and electrical conductivity, protecting against electromagnetic interference and serving as electrodes. Common materials for these coatings include indium tin oxide (ITO) and aluminum-doped zinc oxide (AZO).
- DLC (Diamond-Like Carbon) coatings are nanocomposite layers that mimic diamond, providing low friction, hardness, and corrosion resistance. Deposited via PVD or PACVD processes, they enhance durability in automotive, aerospace, and optical industries using Hydrogenated Amorphous Carbon (a-C:H) and Tetrahedral Amorphous Carbon (ta-C) .
General Specifications of Optical Coatings
Material |
Specifications |
|||||
---|---|---|---|---|---|---|
Substrate |
Surface Figure |
Surface Quality |
Chamfer |
Coating Material |
Clear Aperture |
|
Copper |
Fused Silica, H-K9L, etc. |
– |
40-20 |
0.5mm, 45° |
Ag, Al, Cr, etc. |
> 90% of diameter |
Silver |
Fused silica, BK7 |
< λ/10 @ 632.8nm |
40-20 |
0.5mm, 45° |
Silver |
> 85% of diameter |
Aluminum |
Fused silica, BK7 |
< λ/10 @ 632.8nm |
40-20 |
0.5mm, 45° |
Aluminum |
> 85% of diameter |
Germanium |
Germanium, ZnSe, etc. |
– |
40-20 |
0.5mm, 45° |
ZnS, YbF3, Ge, etc. |
> 90% of diameter |
MgF2 |
Fused Silica, H-K9L, etc. |
– |
40-20 |
0.5mm, 45° |
Al2O3, SiO3, HfO2, Ta@O5, etc. |
> 90% of diameter |
Gold |
Fused silica, BK7 |
< λ/10 @ 632.8nm |
40-20 |
0.5mm, 45° |
Gold |
> 85% of diameter |
Chromium |
Fused silica, BK7 |
< λ/10 @ 632.8nm |
40-20 |
0.5mm, 45° |
Chromium |
> 85% of diameter |
Silicon Dioxide (SiO2) |
– |
PV<λ/4 |
60-40 |
0.2mm, 45° |
– |
>90% of diameter |
Titanium Dioxide (TiO2) |
– |
PV<λ/4 |
60-40 |
0.2mm, 45° |
– |
>90% of diameter |
Fluorides |
– |
PV<λ/4 |
60-40 |
0.2mm, 45° |
– |
>90% of diameter |
Dielectric Coatings |
– |
PV<λ/4 |
60-40 |
0.2mm, 45° |
– |
>90% of diameter |
Diamond-Like Carbon Coatings |
– |
Contact us |
Contact us |
Contact us |
– |
Contact us |
For more details about Avantier’s Optical Coatings,
WE CAN HELP YOU!
Contact us NOW for sales & expert advice.