Silicon Carbide Wafers
Introduction to Silicon Carbide Wafers
Silicon Carbide (SiC) wafers are a specialized semiconductor material known for their high thermal conductivity, high power, and high frequency performance. These wafers are essential in electronic devices requiring high-temperature and high-voltage operations. SiC’s wide bandgap makes it a superior choice for handling higher voltages and extreme conditions compared to traditional materials like silicon.
Applications and Industry Usage
SiC wafers are particularly valuable in power electronics, especially in industries focused on energy efficiency and renewable energy. These wafers are widely used in electric vehicles (EVs) and 5G communication systems, where high power and high-frequency operations are crucial. The high quality and performance of SiC substrates make them ideal for applications that demand reliability under challenging conditions.
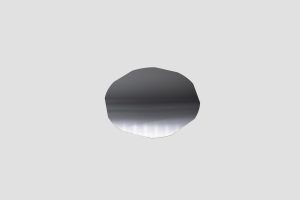
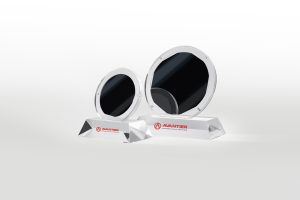
Production Methods: PVT and CVD
The production of SiC wafers involves advanced techniques like physical vapor transport (PVT) and chemical vapor deposition (CVD). In the PVT method, a seed crystal of SiC is placed in a high-temperature furnace, and vaporized silicon and carbon are transported by a carrier gas, typically argon, to form a SiC layer. In the CVD method, silicon and carbon gases react on a substrate at high temperatures, resulting in the growth of a high-quality SiC layer. These methods are designed to minimize defect density, ensuring the production of high-quality wafers.
Wafer Processing and Fabrication
After the SiC crystals are grown, they are sliced into thin wafers and polished to achieve a high degree of flatness and smoothness. These SiC wafers serve as a robust platform for further semiconductor layering, crucial for power devices that require high thermal conductivity and efficient operation. The wafers can be doped to create p-type and n-type regions, essential for fabricating high-performance electronic devices.
Advantages and Limitations of SiC Compared to Silicon
Silicon Carbide (SiC) wafers offer several advantages over silicon, particularly in high-temperature, high-voltage, and high-frequency applications. SiC’s superior thermal conductivity allows it to perform efficiently without the risk of thermal breakdown, making it ideal for power devices in electric vehicles and other high-power applications. Despite these benefits, silicon remains the more commonly used semiconductor material in lower temperature environments due to its simpler preparation process. However, as the demand for energy-efficient solutions in renewable energy and other sectors grows, SiC is becoming increasingly important in the semiconductor industry.
Specifications
Structure | Hexagonal, Single Crystal | |
Diameter | Up to 150mm, 200mm | |
Thickness | 350µm (n-type, 3″ SI), 500µm (SI) | |
Grades | Prime, Development, Mechanical | |
Thermal Conductivity | 370 (W/mK) at Room Temperature | |
Thermal Expansion Coefficient | 4.5 (10-6K-1) | |
Specific Heat (25⁰C) | 0.71 (J g-1 K-1) |
Customization and Expertise
Avantier is one of the leading companies in SiC wafer production, offering customization to meet your specific requirements. Whether you need specialized wafers for high-power, high-frequency, or high-temperature applications, our expertise ensures high-quality results. Contact us for your next project, and let us help you achieve optimal performance with our SiC wafers.
WE CAN HELP YOU!
Contact us NOW for sales & expert advice.