Introduction:
Non-destructive testing (NDT) plays a crucial role in various industries, enabling the evaluation and analysis of materials and structures without causing any damage. Among the various techniques used in NDT, Optical Coherence Tomography (OCT) has emerged as a promising technology. OCT offers numerous advantages over traditional methods such as ultrasound inspection, including higher resolution, faster imaging, non-contact and non-invasive capabilities, and the ability to perform 3D imaging and dimensional analysis. This article explores the potential applications of OCT in NDT, focusing on medical devices, displays and panels, and aviation and automotive industries.
High Resolution and Faster Imaging:
OCT provides exceptional image resolution, typically ranging from 2.6 to 10.0 µm. This high resolution enables the detection and characterization of even the smallest defects or anomalies within the inspected material. Compared to ultrasound inspection, OCT delivers more detailed and precise images, allowing for improved defect identification and analysis.
Additionally, OCT offers faster imaging capabilities, enabling real-time or near-real-time inspection. The rapid acquisition of images enhances the efficiency of NDT processes, reducing inspection time and enhancing overall productivity.
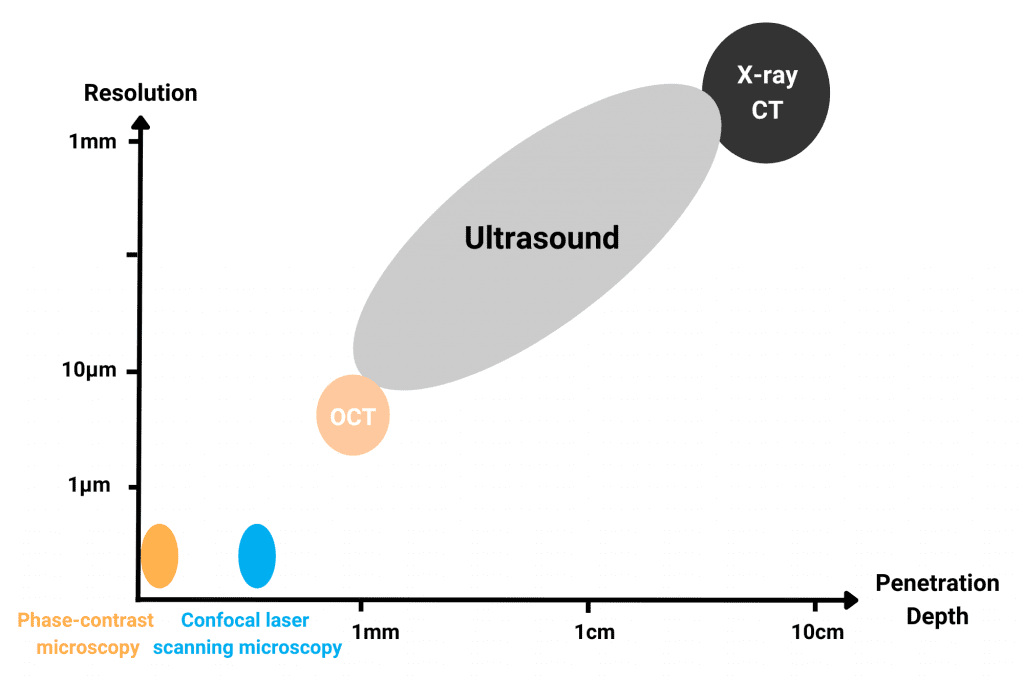
Non-Contact and Non-Invasive:
One of the key advantages of OCT is its non-contact and non-invasive nature. Traditional NDT techniques often require physical contact with the material being inspected, which can potentially cause damage or alteration. OCT eliminates this concern by employing light waves for imaging, ensuring that the inspected object remains intact and undisturbed.
This non-contact approach is particularly beneficial when dealing with delicate or sensitive materials, such as medical devices or fragile electronic components. OCT allows for thorough inspection without compromising the integrity of the object, making it an ideal choice for quality control and assurance.
3D Imaging and Dimensional Analysis:
OCT enables the acquisition of three-dimensional images, providing a comprehensive view of the internal structures and defects within an object. This feature is invaluable in NDT, as it allows for a thorough analysis of the material’s integrity and dimensional characteristics.
By capturing volumetric data, OCT enables precise measurements, facilitating dimensional analysis and defect quantification. This capability proves highly useful in industries where accurate measurements are crucial, such as aerospace and automotive manufacturing.
Applications of OCT in Non-Destructive Testing:
1. Medical Devices:
OCT has found extensive applications in the inspection and quality control of medical devices, including micro optics and aspheres. It enables the assessment of implantable devices, such as stents and prosthetics, ensuring their structural integrity and dimensional accuracy. Furthermore, OCT aids in the examination of biomaterials, detecting any manufacturing defects or material inconsistencies related to medical optics.
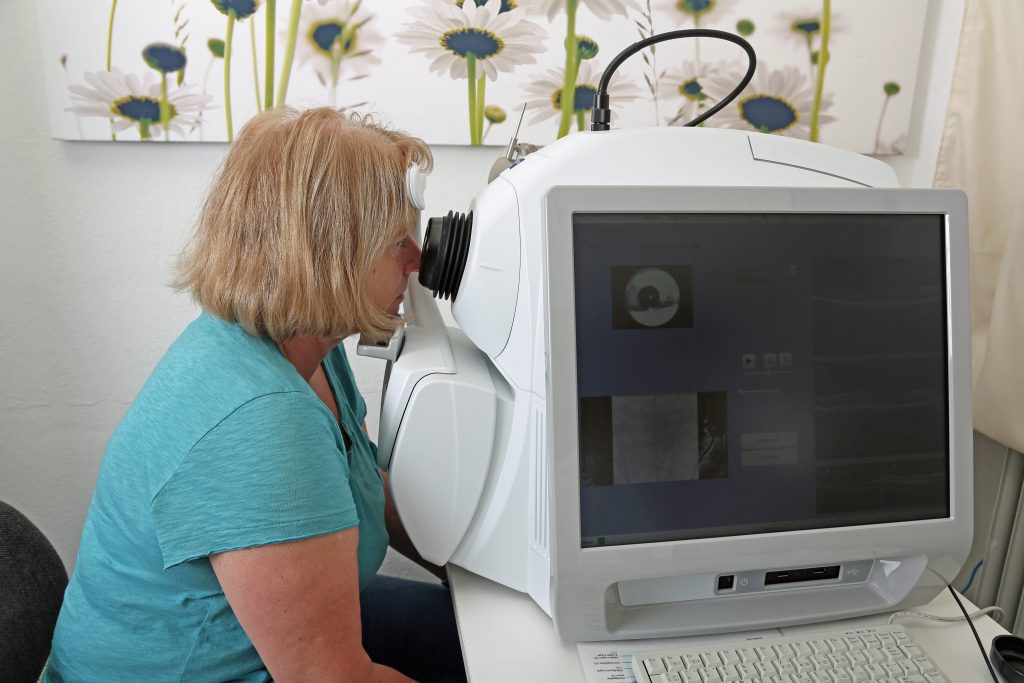
2. Displays and Panels:
The display industry benefits greatly from OCT in NDT. It enables the evaluation of display panels, such as LCD and OLED screens, ensuring their uniformity, pixel integrity, and absence of defects. OCT’s high resolution and fast imaging capabilities prove essential in identifying small imperfections or performance issues.
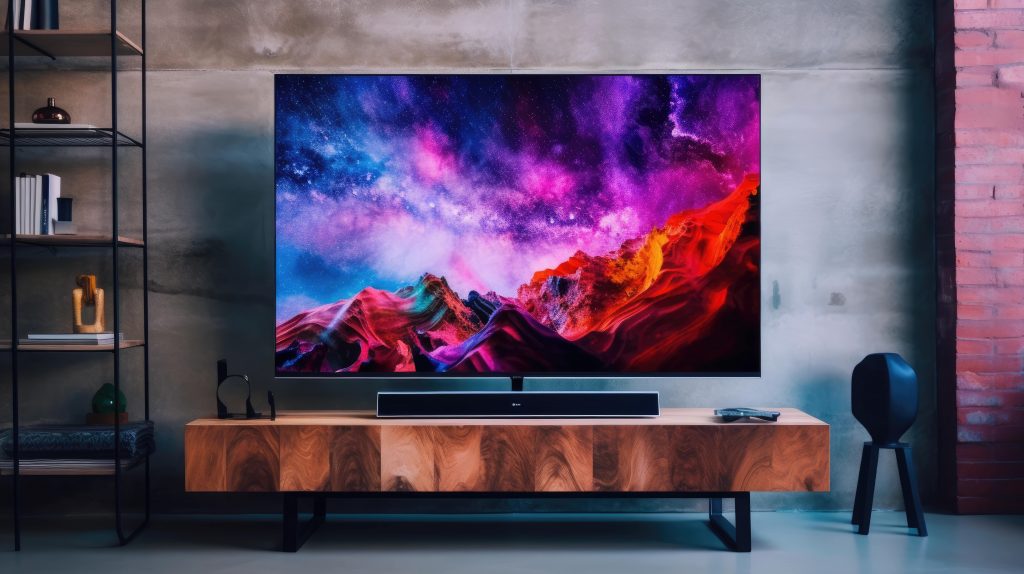
3. Aviation and Automotive:
In the aviation and automotive sectors, OCT plays a significant role in NDT. It assists in inspecting critical components, such as turbine blades, engine parts, and composite materials, for any structural abnormalities or hidden defects. By detecting such issues early on, OCT helps ensure the safety and reliability of these vital systems.
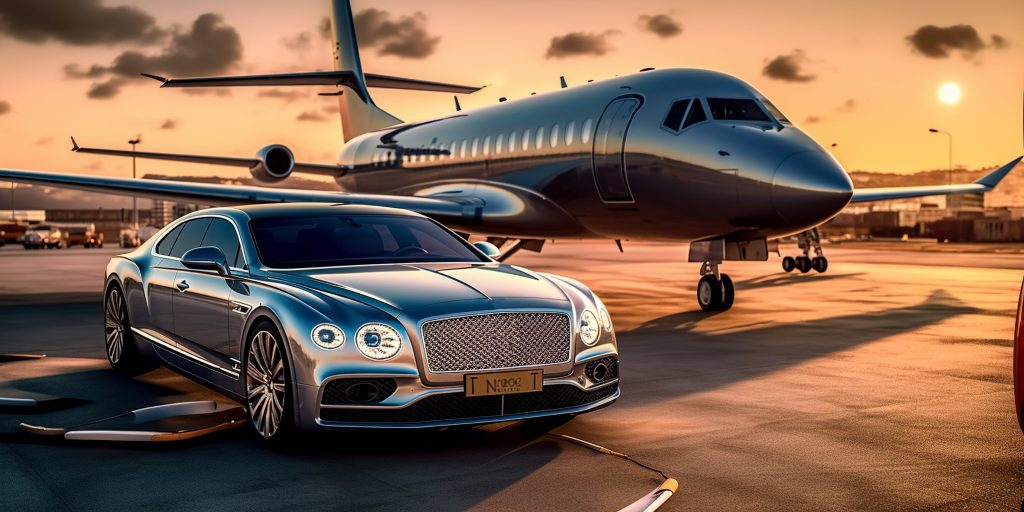
Conclusion:
Optical Coherence Tomography (OCT) has emerged as a powerful tool in non-destructive testing, surpassing traditional techniques like ultrasound inspection in many aspects. Its high resolution, faster imaging, non-contact nature, and 3D imaging capabilities offer significant advantages across various industries. OCT finds applications in the evaluation of medical devices, displays and panels, as well as aviation and automotive manufacturing. With ongoing advancements in OCT technology, we can expect further improvements in NDT processes, ultimately enhancing quality control, product reliability, and safety standards across industries.
GREAT ARTICLE!
Share this article to gain insights from your connections!