Key Takeaways:
- Reflective optics, essential for fields like astronomy, life sciences, and industrial applications, utilize mirrors to direct wavefronts.
- Mirrors are either first surface, with coatings on the front, or second surface, with coatings on the back, affecting their use in precision optics.
- Reflective coatings can be metallic, dielectric, or hybrid, tailored for durability and reflectivity.
- Compared to refractive systems, reflective optics are simpler, more cost-effective, and ideal for laser focusing and multispectral imaging due to minimal dispersion and absorption issues.
Reflective optics are key to many industrial and life science applications, as well as astronomy and high-energy physics. Essentially, reflective optics is the optics of mirrors: smooth reflective surfaces that change the direction of a wavefront.
In many cases, reflective optical systems provide a simpler, more affordable option when contrasted with refractive systems. That’s especially the case if you’re doing laser focusing with multispectral imaging. We’ll look at why in a moment. But first, just what is a mirror, how are they made, and how do they work?
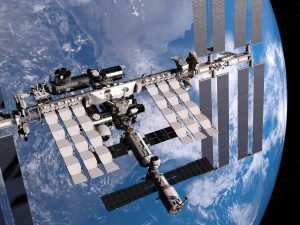
Understanding Reflective Optics: The Science of Mirrors
What is a mirror?
At its simplest, a mirror is a reflective surface. Light that hits a mirror bounces back in the opposite direction. The law of reflection tells us that the angle of incidence at which a ray of light hits a mirror is equal to the angle of reflection; the angle at which the ray of light leaves the surface.
Mirrors can be manufactured in different shapes and sizes, with surfaces of varying qualities and various reflectivity levels. As a mirror is typically manufactured from an optical flat with a reflective coating, there are two types of mirrors, depending on the placement of the coating: first surface and second surface mirrors.
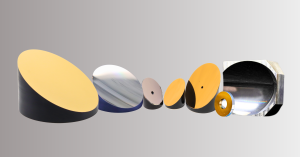
For a first surface mirror, the high reflectance coating is applied to the front surface of the mirror. The substrate may be glass, metal, or other semiconductor substrates. The substance used will have no effect on reflectivity as the light is reflected before it reaches the substrate.
In a second surface mirror, the high reflectance coating is applied to the back surface of the mirror. The substrate of a second surface mirror is typically a highly transparent substance such as glass, since the light must travel through the substrate before it is reflected by the coating. The benefit of this configuration is that the coating is protected by the optical substrate. This geometry, however, does lead to image distortion, so it is not usually used in precision optics.
Mirror Coatings for Reflective Optics
Physical vapor deposition, chemical vapor deposition, and sputter deposition are three important techniques used to create the mirror coatings which give reflective optics their special qualities. All of these processes can be used to create ultra-thin layers that are smooth, uniform, and essentially defect-free.
The coating used will determine both the reflectivity and the durability of the final mirror. Reflective coatings may be metal, dielectric, or a combination of the two. Metal coatings such as gold, silver, and aluminum are highly efficient reflectors, but they are also very delicate. When coated with a dielectric overcoat, they are more durable. Dielectric coatings— stacks of numerous ultra-thin layers of varying refractive index—- can also be used alone. Though the material used in each layer is not reflective on its own, constructive interference of reflected light at each interface results in high reflectance for certain wavelengths.
Dielectric coatings are more flexible than metallic coatings, and they are also more durable and less prone to laser damage. They cannot used over as broad a wavelength of light as metal coatings, however, and must be designed for specific narrow spectral bands, usually in the visible and NIR regions.
Why Choose Reflective Optics?
If you’re working with laser focusing and multispectral imaging applications, refractive lenses have some potential problems. Dispersion is one of them. Since the speed of light passing through a lens is wavelength dependent, dispersion keeps different wavelengths from focusing at one point. Optical designers get around this problem by using compound lenses. In a compound lenses, different elements with specific materials are used to cancel out dispersion.
But a compound lens is only effective at reducing dispersion over a limited spectral band. As the band increases in width more and more elements are required. If you want to correct the dispersion in the system further, you’ll also need more elements. It gets very complex and very expensive very quickly.
That’s not the only problem with the use of refractive systems for laser focusing and multispectral imaging. The other involves absorption. If you’re working with high laser power you know that even the absorption of a small percentage of optical energy will lead to catastrophic lens failure. You get around this by choosing substrates and coatings so transmission is maximized at your laser wavelength.
This works well— when you’ve got a narrow laser band. But what happens when you need both high power laser and multispectral imaging? The wider the waveband, the lower the transmission of your coatings. The only reasonable workaround is again to use several sets of compound lenses, an unwieldy and costly solution.
Reflective optical systems are essentially wavelength independent, and reflection does not induce dispersion. A typical reflective system for laser focusing and multispectral imaging will not include many elements, and it can be made compact and rugged. It’s significantly cheaper than the complex workaround solutions meant to solve the problems with diffraction and absorption of refractive systems, and it’s easy to modify if the need arises.

Reflective Optics at Avantier
At Avantier, we produce custom-made, high-performance reflective optics for our clients in a wide variety of fields. Extensive manufacturing abilities and state-of-the-art metrology enable us to produce almost any optic you might need. Contact us today to set up an initial consult or learn more about reflective optics at Avantier.
GREAT ARTICLE!
Share this article to gain insights from your connections!