Mastering the F-theta Scanning Lens – Part 2
Field Characteristics of F-theta Scanning Lenses:
In the realm of F-theta scanning lenses, the scanning angle dictates their field of view crucial for laser operations, with a prevalent trend towards larger angles to accommodate expansive working surfaces. This evolution, however, amplifies demands on optical systems, emphasizing the need for precision and consistency, particularly in the wide-angle F-theta lenses ideal for applications requiring extensive coverage.
- Scanning Angle as Field of View:The scanning angle of the F-theta scanning lens determines its field of view. This parameter is crucial for laser engraving, cutting, or marking operations, as it defines the area that the lens can effectively cover.
- Large Field of View: F-theta scanning lenses typically have a large field of view exceeding 20 degrees. There is a growing trend in lens development toward achieving larger field angles. This is driven by the desire to accommodate larger working surfaces and enhance the versatility of the lens in a variety of applications.
- Increasing Demands on Optical Systems: As field angle expands, it places increasing demands on the optical system associated with the F-theta lens. As the scanning angle increases, the optical system must meet stricter requirements to achieve precision and consistency across the entire viewing field.
- Common Scanning Angles: In the current market, F-theta lenses typically have scanning angles of less than 60 degrees. A lens with a scanning angle ranging between 50 and 60 degrees is categorized as a wide-angle F-theta lens. This rating signifies that the lens can cover a wide field of view, making it ideal for applications that demand a greater range.
Aperture of F-theta Scanning Lens
In the exploration of F-theta scanning lenses, the entrance pupil aperture emerges as a pivotal component, intricately linked to the laser beam diameter. Its meticulous alignment not only influences the characteristics of the focused beam but also plays a critical role in ensuring optimal functionality, precision, and reliability in laser engraving, cutting, and marking applications.
- Entrance Pupil Aperture: The entrance pupil aperture of the F-theta scanning lens plays a crucial role in the system. It is linked directly to the beam diameter of the laser. As it is responsible for determining the size of the laser beam that enters the lens, it affects the characteristics of the focused beam and subsequently, the overall performance of the optical system.
- Beam Diameter Relationship: The relationship between beam diameter and aperture is significant. The entrance pupil aperture is meticulously crafted to align with the laser beam diameter utilized with the F-theta lens. Proper alignment between the aperture and laser beam diameter is critical for optimal lens functionality and precision in laser engraving, cutting, and marking applications.
- Precision in Laser Focusing: By precisely defining the entrance pupil aperture, the F-theta scanning lens effectively focuses the laser beam for precise and controlled material processing. Aligning the aperture with the laser beam diameter also enhances the overall performance and reliability of the optical system.
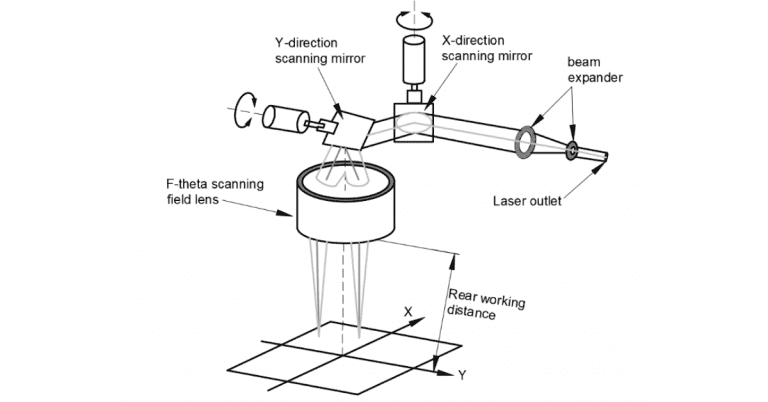
Working Distance and Flange Distance in F-theta Scanning Lenses
The front and rear working distances in F-theta scanning lenses, intricately influenced by galvanometer positioning, play a dynamic role in beam manipulation. A shorter rear working distance proves essential for achieving precise laser focus and uniform machining across the entire working surface, while the flange distance emerges as a crucial parameter, impacting structural design, mounting considerations, and overall alignment for optimal optical system functionality.
Front and Rear Working Distance:
- Front Working Distance: The front working distance of the F-theta scanning lens is associated with the entry pupil distance, and it is influenced by the position of the galvanometer. The galvanometer’s location affects the front working distance, highlighting the interplay between the lens and the beam manipulation system.
- Rear Working Distance: In contrast, the rear working distance refers to the distance from the lens to the working surface. This distance is a critical parameter, especially for achieving uniform machining across the entire working surface. A shorter rear working distance is generally desirable, as it allows for efficient and precise laser focusing.
Flange Distance: The flange distance in F-theta scanning lenses is defined as the distance between the lens mounting end face and the working face. This parameter is a crucial consideration in the structural design of the optical system. It influences the overall size and configuration of the system and is essential for ensuring proper alignment and functionality.
Working Distance:
- Galvanometer Influence: The front working distance, linked to the galvanometer’s position, emphasizes the dynamic nature of F-theta lenses in response to beam manipulation requirements.
- Uniform Machining: The rear working distance’s importance in achieving uniform machining underscores its role in maintaining consistent laser focus across the entire working surface.
Flange Distance in Structural Design:
- Mounting Considerations: The flange distance is integral to the mounting and integration of the lens into the optical system.
- Alignment and Configuration: Proper consideration of the flange distance ensures correct alignment of the lens and contributes to the overall configuration of the optical setup.
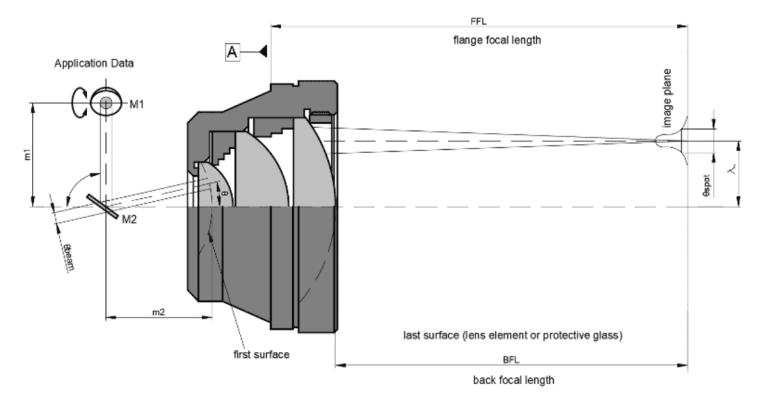
Telecentricity in F-theta Scanning Lenses
The telecentricity challenge in F-theta lenses, characterized by a lack of uniform focus across the entire field, introduces inconsistencies in precision machining. While a telecentric field lens resolves this issue by ensuring perpendicular light rays, its adoption entails trade-offs, including increased lens size and heightened design complexity, highlighting the delicate balance between achieving consistent focus and managing the associated drawbacks in laser applications.
- Telecentricity Issue in F-theta Lenses: An inherent problem with F-theta lenses is the lack of telecentricity. In these lenses, the laser beam at the center of the field is focused vertically onto the machining plane, while the laser at the edge is tilted. This results in a round light spot at the center and an elliptical light spot at the edge.
- Inconsistency in Precision Machining: The consequence of this telecentricity issue is the inconsistency between the center and edge effects during precision machining. The round light spot at the center contrasts with the elliptical light spot at the edge, impacting the uniformity and accuracy of the laser processing across the entire working surface.
- Solution: Telecentric Field Lens: To address this problem, a telecentric field lens is employed. Telecentric lenses ensure that the light rays strike the machining plane at right angles, regardless of their position within the field of view. This leads to a consistent focus across the entire working surface.
- Disadvantages of Telecentric Lens: While a telecentric field lens resolves the telecentricity issue, it comes with drawbacks. The use of a telecentric lens tends to increase the size of the lens, impacting the overall dimensions of the optical system. Additionally, the design complexity of telecentric lenses is higher, posing challenges in their engineering and manufacturing.
- Trade-offs: The decision to use a telecentric lens involves trade-offs between achieving consistent focus throughout the field and managing the increased size and design complexity. These considerations depend on the specific requirements of the laser application and the importance of telecentricity for precision.
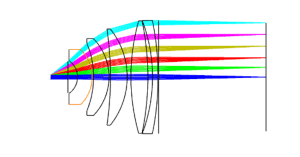
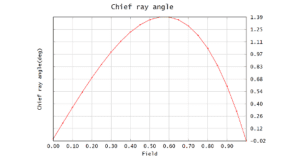
Telecentric F-theta lens
Laser Damage Threshold in F-theta Scanning Lenses
The laser damage threshold becomes a critical focal point in the design and material selection for F-theta scanning lenses, particularly due to their common utilization with high-power lasers in applications like engraving and cutting. The lenses, designed to withstand intense laser energy, often leverage robust materials such as quartz, chosen for its exceptional damage threshold. This consideration significantly shapes both lens design and coating processes, ensuring durability and resistance to laser-induced damage in demanding applications.
- Consideration of Laser Damage Threshold: The laser damage threshold is a crucial consideration in the design and selection of materials for F-theta scanning lenses. This importance arises from the fact that these lenses are commonly used in conjunction with high-power lasers, especially in applications such as laser engraving and cutting.
- High-Power Laser Usage: F-theta lenses are designed to handle the intense energy generated by high-power lasers. The laser damage threshold defines the maximum level of laser energy that the lens can endure without sustaining damage.
- Material Selection: In response to the need for a high laser damage threshold, some F-theta lenses are crafted from materials known for their robustness and resistance to laser-induced damage.
- Quartz as a Material Choice: Quartz is one such material that is often chosen for its exceptional laser damage threshold. F-theta lenses made from quartz can withstand high-energy laser beams, making them suitable for demanding applications.
- Impact on Design and Coating: The consideration of the laser damage threshold influences both the lens design and the coating process. Designs need to account for the potential intensity of laser exposure, and coatings may be applied to enhance the lens’s durability under high-power laser conditions.
Lens Performance
Beam convergence stands as a crucial performance metric for F-theta scanning lenses, determining their ability to efficiently focus laser beams onto the working surface for high-resolution applications. Operating near the diffraction limit, these lenses emphasize optimal beam convergence to approach theoretical resolution limits. Uniformity across the working surface, achieved by minimizing variations in light spot sizes, becomes pivotal for consistent and accurate results in precision machining, engraving, and cutting. The significance of these factors directly influences the quality of laser applications, while the pursuit of optimal convergence and uniformity presents ongoing design and engineering challenges for manufacturers adapting to evolving demands in laser technology.
- Beam Convergence:
- Key Performance Metric: The degree of beam convergence is a paramount performance metric for F-theta scanning lenses. It refers to the ability of the lens to focus the laser beam efficiently and precisely onto the working surface. Beam convergence is vital for achieving high-resolution and detail in laser-based applications.
- Close to the Diffraction Limit: F-theta lenses are expected to operate close to the diffraction limit, which is a fundamental limit defining the best possible resolution achievable by an optical system. This requirement emphasizes the need for optimal beam convergence to ensure that the focused laser beam approaches the theoretical limits of resolution.
- Uniformity:
- Uniformity Across the Working Surface: Another critical aspect of lens performance is the uniformity of the laser beam across the entire working surface. This requires minimizing variations in the size and intensity of the light spot between on and off-axis positions.
- Small Gap in Light Spot Sizes: Achieving uniformity involves maintaining a small gap between on-axis (center) and off-axis (edge) light spot sizes. A small gap ensures that the laser energy distribution remains consistent, leading to uniform results during precision machining, engraving, or cutting operations.
- Significance for Applications:
- The performance of F-theta scanning lenses directly impacts the quality and precision of laser applications. High beam convergence and uniformity contribute to achieving detailed, consistent, and accurate results across the entire working area.
- Optimization Challenges:
- Achieving optimal beam convergence and uniformity poses design and engineering challenges. Engineers and manufacturers continually strive to enhance lens designs, coatings, and manufacturing processes to push the limits of performance and meet the demands of evolving laser applications.
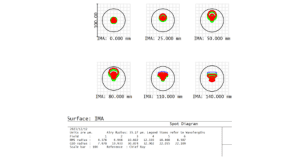
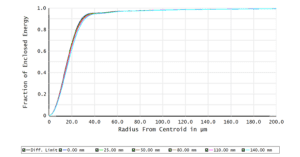
Simulation performance of the F-theta lens
In the comprehensive exploration of F-theta scanning lenses in “Mastering the F-theta Scanning Lens – Part 2,” we’ve delved into the intricate field characteristics, from scanning angles defining the field of view to the challenges of telecentricity and laser damage thresholds. The examination of aperture adventures, working distances, and telecentricity elucidates the dynamic interplay of these lenses within optical systems. The quest for optimal beam convergence and uniformity, detailed in the lens performance symphony, sheds light on the critical metrics influencing precision in laser applications. As manufacturers navigate optimization challenges, this journey concludes with a call to push the boundaries, emphasizing the evolving landscape of F-theta scanning lenses in the pursuit of excellence in laser technology.
For fundamental information, refer to the F-theta Scanning Len Part 1.
GREAT ARTICLE!
Share this article to gain insights from your connections!